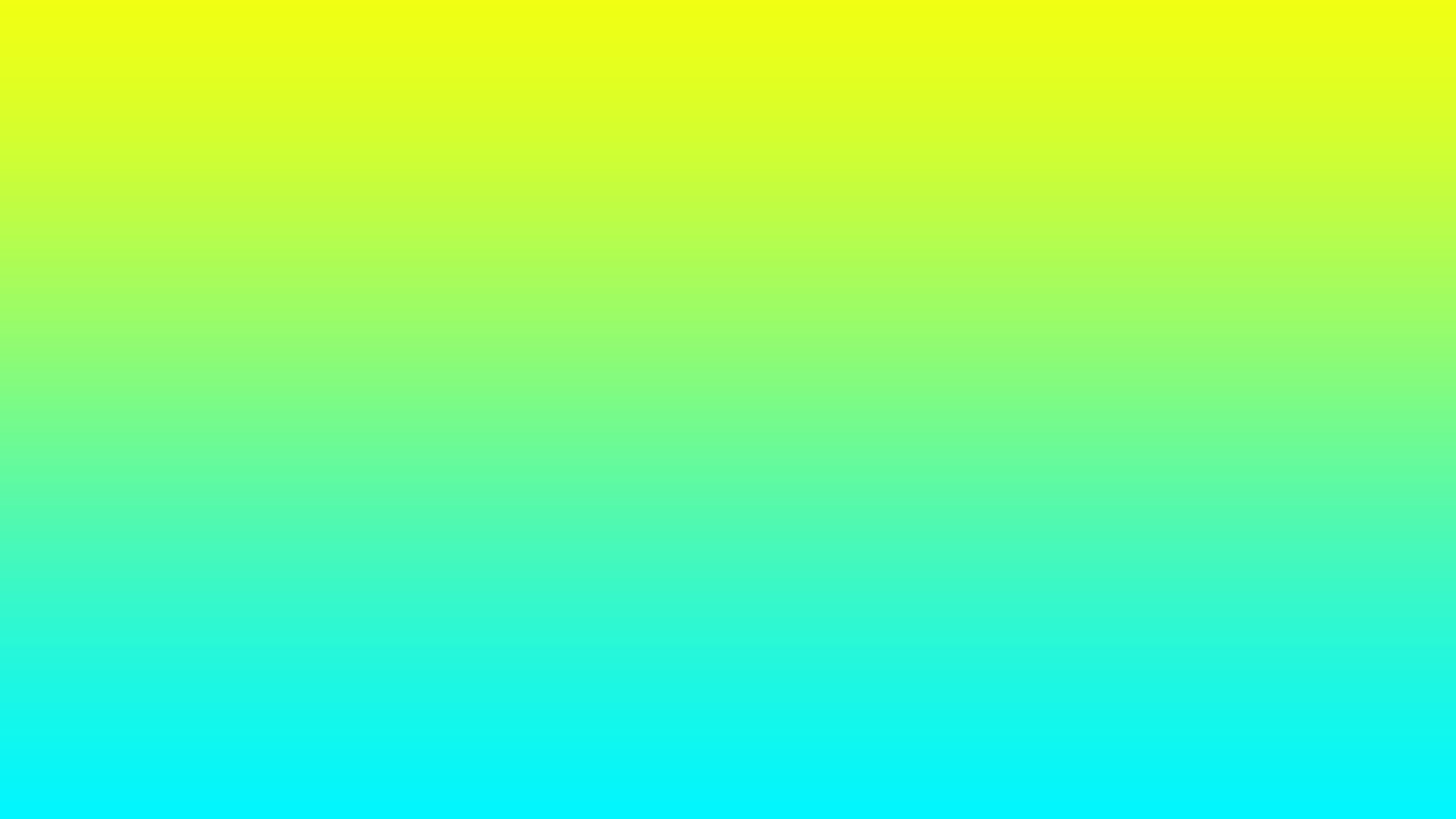
CAPITAL
There are several different steps that go into making a Snapple drink. One of the first steps is creating the packaging the Snapple drinks will be sold in. Snapple’s bottles are made from recycled bottles and old glass and created into new ones with a specific process. At the Salem Ardagh Glass Plant in New Jersey, there are large piles of plastic bags, caps, and broken glass. The plant sorts through these piles and isolates all of the glass. A big magnet is used during this step in order to pull out pieces of metal like lids, cans, or caps. At this point in the process, there are smaller piles of glass that need to be sorted by color. To make the Snapple bottles there can only be clear glass. The plant uses a optical sorting machine to take pictures of the glass. They then use air jets to blow the desired pieces of glass onto a conveyer belt where they will continue the process. The next steps consist of melting all the clear glass. The glass is taken to a furnace in the factory that is heated to 2,700 degrees. The glass is then mixed with sand, limestone, and soda ash. More melted glass is added to the mix due to a small amount of recycled glass that can be used. The next step of the process is cutting up the pieces of molten glass using industrial machines. Next each piece of molten glass is poured into a mold that creates the mouth of each bottle. Then a glass- blowing machine blows the bottles to finalize them. The finished product is about 20 to 25% recycled glass. The Salem Glass Plant can produce 400 snapple bottles a minute with a recent upgrade of machines. The factory ships the bottles of Snapple six days a week. They are able to produce about 3 million a day (http://www.npr.org/sections/money/2013/06/11/190668206/how-a-used-bottle-becomes-a-new-bottle-in-6-gifs).
The Snapple bottle caps are made of a tinplate material. An interesting fact is printed on the back of every cap for the consumer to enjoy (http://ems02003.egain.net/system/selfservice.controller?CONFIGURATION=1000&PARTITION_ID=1&TIMEZONE_OFFSET=&CMD=VIEW_ARTICLE&ARTICLE_ID=2670&SIDE_LINK_TOPIC_ID=&SIDE_LINK_SUB_TOPIC_ID=&EXPANDED_TOPIC_TREE_NODES=&TOPIC_ID=).
The owner of Snapple, the Dr. Pepper Snapple Group, has 21 different manufacturing centers located throughout North America. There are also more than 115 distribution centers. There also hundreds of third party distributors and bottlers. The main center of distribution is located in the Mojave Desert. This is an 851,500 square foot office facility as well as a production warehouse. This center has 44 different truck docks in their 544,000 square foot area of warehouse. They also have 267,000 square feet of production area that contains five bottling lines. They also have 40,000 square feet of office space (http://askbrinkmann.com/success-stories/industrial/dr-pepper).
The company started off in a small health food store in New York. It has since grown into a recognized company throughout the world. Snapple has been owned by different companies but is now part of the number one flavored carbonated soft drink company in North America (http://www.drpeppersnapplegroup.com/company/history/).
The Dr. Pepper Snapple Group has an average capital cost of 6.87%. The companys return on invested capital is about 17.09%. The Dr. Pepper Snapple Group has higher returns on investments than the cost of their company to increase the capital needed for investments. The company expects to see the value and size increase (http://www.gurufocus.com/term/wacc/DPS/Weighted+Average+Cost+Of+Capital+(WACC)/Dr+Pepper+Snapple+Group+Inc).



